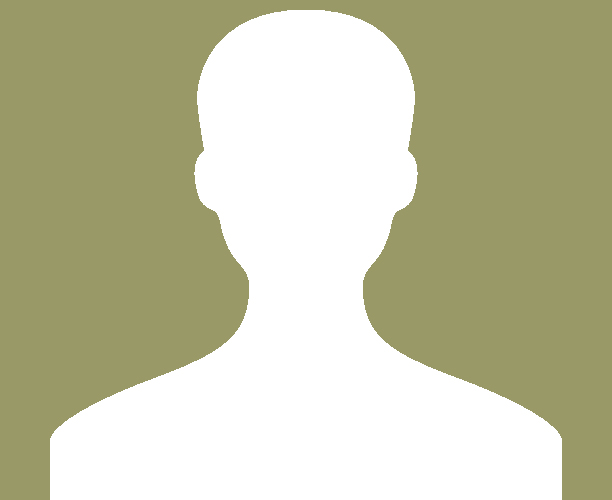
Views:321 Applications:41 Rec. Actions:Recruiter Actions:4
Chief Manager - Dipping (10-15 yrs)
Position: Dipping
Qualification: BE / B.Tech chemical/rubber/textile/polymer technologists having the dipping experience
Experience: within 10 to 15 yrs or less than 20 yrs ideally, however, we can deviate if exp is good.
Position : Manager / Chief manager
CTC: 20 - 25 Lpa
The skill set is - continuous process industry. Experience of dipping either in industrial or belting fabrics or in tire companies where primary role is of dipping. Else we can also target companies like CUMI where they have the different type of dipping for abrasive belts. Or from a textile industrial fabrics industry where dipping or impregnation of the textile fabric is adopted as the main process.
Position Name Chief Manager - Dipping
Department Dipping
Reporting To Plant Head
Purpose
To Plan and achieve quality production & packing of Dipped fabric, economically and safely.
Principal Accountabilities & Responsibilities :
Accountabilities Responsibilities :
1. Adherence to monthly production plan
- Preparation of plan on the basis of the requirements given by PPC keeping in view the available resources (transfer of greige fabric, chemicals & packing materials.
- Reviewing & monitoring of plan vs actual
- Taking corrective action for the shortfalls.
2. Striving for continuous reduction in production cost without degradation of Quality
- Identification of priorities issues and taking projects & themes.
- Preparing activity schedules and assigning responsibilities to the project team members.
- Facilitating the team in completion of the improvement projects.
- Continuous updating of quality control process charts with improvements & better work practices
- Continuous updating of process FMEA with improvements projects & trouble shooting methods
3. Ensuring strong system for addressing and eliminating customer complaints
- Establishment of system for dipping operation
- Establishment of system process control
- Systematic analysis of problems & Root cause analysis
- Detailed analysis of the complaints of the customers and finding the causes of the same.
- Rectification of the problems and taking preventive steps to ensure non-repetition of the same.
- Providing the complete feedback to the customer on the complaint.
- Visiting the customer to educate on various process control parameters etc. being adopted to ensure quality product.
4. Ensuring capability development of the team
- Training & skill development
- Preparation of training & trouble shooting manuals
- Conducting technical training for the employees
- Implementation of the development plan for the team members.
- Review & update on skill matrix
5. Ensuring safe operations of the production facility
- Identifying unsafe acts, conditions & eliminating
- Creating awareness on safe working condition
- Ensuring employees adhere to the safety policy of the unit
- Counseling & recommending disciplinary action against the employees for non-adherence.
6. Approval of new products as per customer requirements
- Developing trial plans & process parameters for new products
- Establishing system for new product development from trial phase to standardization phase
7. Effective utilization of LPG
- To identify and eliminate the leakage of hot air at various zones
- Identify the defect burners and arrange for replacement through maintenance department
- Adherence to preventive maintenance schedule of burners
- Check for effective insulations and arrange for replacement of defective insulations
8. Effective utilization of Chemicals
- Plan for procurement of Chemicals
- Plan for proper storage of Chemicals
- Maintain minimum inventory of Chemicals
- Directing the workmen for Proper use PPE's during handling of Chemicals
- Educating the workmen about the Chemical properties of the chemicals and steps to be adopted during emergencies
9. Implementation of system and processes in Dipping area.
- Adherence to ISO standards
- Adherence to OHSAS systems
- Managing in TQM way of working.
- Implementation of process related checks
10. Contributing to various department level BM/DM themes in twisters
- Identifying area of improvements
- Taking of PSP projects for improvements
11. System and Procedures
- Making of QCPC / Formats / Procedures for a manufacturing process.
- Implementation of safety systems to achieve Zero accident target
12. Ensuring Reduction of downgrades
- Monitoring downgrades and initiating countermeasures to reduce wastes
- To guide the team to implement countermeasures to reduce downgrade
- To ensure operating process conditions to avoid any deviations in the process which may result in downgrades
13. I/O Ratio
- Effective utilization of dipping Chemicals, LPG as per the norms specified in the standards
- Reduction of waste and substandard
14. Power Control
- To reduce ideal running of dipping machine
- Effective startup of temperature control system
Working Relationships :
Purpose of interaction Frequency (How often)
Internal Customer:
1. MLT
2. QA
- On time production of dipped fabric for dispatches.
- To discuss and find a solution to overcome processing and properties related problems.
- Daily / As and when required.
Internal Suppliers.
1. Utility.
2. Mechanical maintenance.
3. Electrical
4. Automation
Utility:
1. To maintain chilled water supply desired temperature. Mech / Elect/ Auto :
- Ensure that all PM related jobs are carried out as per schedule.
- Identify the area of repeated problems and work out to find corrective measures to overcome problems.
- Making standards to improve process reliability and uniform work pattern.
- Discuss reasons for breakdowns to identify root cause and preventive measures.
As and when required and discussed during SAM meeting.
Business Sourcing Team :
1. Understanding DF customer schedules and provide commitment in line with the Indent
2. To discuss and find solutions to achieve deliveries in time.
- As and when new plan & schedule is received
- Weekly to review Plan Vs actual DF production.
MLT team
1. DF delivery status.
2. PPC related matter
3. Specification release & vendor feed back
Dipping MT
1. List of issues
2. communication of new developments
3. Customer complaints.
4. Customer needs.
5. Change in work pattern.
As and when required.
MT head
1. Discussion of commitment to indent.
2. Issues related to process and IR.
3. Monthly report
When indent is received
AT/MIS
1. Material balance and WIP.
2. For BCR input.
3. For budget
IPST / HR
1. For training needs
2. TQM activity
Decision-making Boundaries :
- Decisions on manufacturing-related expenditures
- Deciding product specifications, Standard Operating Conditions
- Deciding on purchase of raw materials and packing materials
- Recommend budgets for Textiles Function
- Can recommend promotions and compensation based on performance of team members
- Can approve team members for internal/external training
- Can approve tour plans for MT members for participation in various competitions & visits
- Can approve improvements changes in manufacturing area for improving quality and machine efficiencies.
- Plan for growth opportunities to team members.
Position Specification:
- Educational Qualification BE / B.Tech (Chemical/ Rubber Tech)
- Duration of experience 12-15 years
- Nature of experience Manufacturing field with knowledge on processing of technical textile fabrics
- Experience in handling dipping process
This job opening was posted long time back. It may not be active. Nor was it removed by the recruiter. Please use your discretion.